In the pharmaceutical, biotechnology and agri-food industries, production, maintenance and laboratory operators regularly talk about sterilising filtration and, more specifically, 0.22 µm filters (0.22 micron filters) or sterilising filters.
Questions about sterilising filtration:
- What does sterilising filtration mean?
- How do you describe a 0.22 µm filter?
- When is a filter considered absolute?
- What can an integrity test prove?
These are just some of the questions that come up when we talk about sterilising filtration. The questions are easy, but the answers are much harder, especially as the terms used have become increasingly generic. Many industries use 0.2 µm filters, but only the pharmaceutical and biotech industries have the specifications that 0.2 µm filters must meet. Suppliers sometimes deliver 0.2 µm filters with certificates but these elements do not meet the standards imposed by the pharmaceutical and biotech industries.
Let's take a look at this vast subject.
History: the origin of the concept of sterilising filtration
In the 1970s, a group of major pharmaceutical companies and filter manufacturers set up an organisation called HIMA (Health Industry Manufacturer's Association). One of the first actions taken by this organisation was to define the criteria that a sterilising filter should meet. In the 1970s, a 0.45µm filter was considered to be a sterilising filter. But as analytical methods became more refined, using only the retention threshold of a filter to define the notion of sterilising filtration or sterility was a little empirical and not necessarily representative or sufficient.
HIMA therefore created a very detailed challenge that would become the benchmark against which sterilising filters had to be measured in order to be considered as sterilising in the pharmaceutical industry.
Bacterial challenge for a sterilising filter
The challenge was developed using a micro-organism called Pseudomonas Diminuta (ATCC19415), which has now been replaced by Brevundimonas Diminuta (ATCC19146). This reference micro-organism is approximately 0.3 µm wide and 0.8 µm long. The challenge also describes the culture medium to be used to grow it, at what temperature and for how long. The HIMA challenge defines a concentration and quantity of this bacterium to test the filter with a precise quantity of micro-organisms per cm². 0.2 µm or 0.22 µm then became a label but did not mean that all manufacturers of sterilising filters could pass the HIMA tests. Filter manufacturers with HIMA-validated products found themselves competing with non-HIMA-approved filters, and in non-critical markets (solvents, half-water, acids, etc.) were forced to develop cheaper product ranges. To remain credible and to be able to differentiate between these 2 families of filters without difficulty, manufacturers called the filters validated by the HIMA challenge absolute 0.2 µm filters or 0.22 µm filters. Today, the HIMA standard has been replaced by ASTM Standard F838-83. The test procedures have remained the same, only the names and the organisation have changed .
Example of sterilising cartridges
Bacterial challenge: HIMA and ASTM 838-83 standards
The ASTM F838-83 standard entitled ‘Determining Bacterial Retention of Membranes Filters Utilized For Liquid Filtration’ is the new reference replacing the HIMA (Health Industry Manufacturer Association) test entitled ‘Microbiological Evaluation of filters for sterilizing liquids’. The reference micro-organism for ASTM is Brevundimonas Diminuta (ATCC19146) (diameter 0.3 µm - length 0.6 to 0.8 µ) and for HIMA, Pseudomonas Diminuta (ATCC19415) (diameter 0.3 µm - length 1 µm) cultured in a Lactose Saline solution according to the parameters described in the procedure. This micro-organism was selected because of its very small size obtained in culture under stress or lack of food. The filter membrane must meet a minimum challenge of 107 organisms per cm² of effective filter surface.
Once the challenge solution has been prepared, the filter membrane is installed in the filter housing and the whole system is autoclaved. After cooling, the sterility of the system is checked and the integrity test can take place. The solution is filtered through the test membrane filter and the control filters. When all the test solution has been filtered, the control filters are placed in 150mm Petri dishes containing Soybean Casein Digest Agar. All colonies growing are then counted and identified.
The log reduction value (LRV Log Reduction Value) is calculated as follows:
LRV = log10= Number of micro-organisms in the challenge / Number of micro-organisms in the filtrate
Brevundimonas (Pseudomonas) diminuta zoom 3000x
Here's a summary of what you need to know about sterilising filtration:
Do you want to optimise a sterilising filtration process or are you looking for equipment with absolute filters?
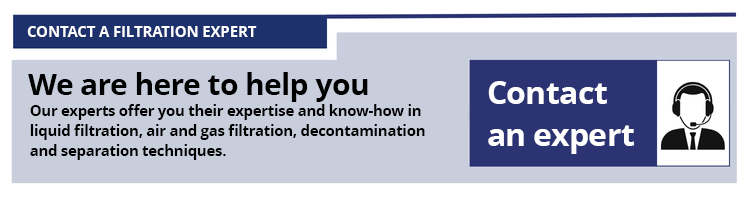