Filters used in the API manufacturing process must be compatible with all the chemicals and solvents used in the production line. If there are no contraindications, stainless steel filter bodies are preferred. However, some syntheses require the use of solvents that are not compatible with stainless steel filtration equipment. What are the alternatives?
Apply a polymer coating to stainless steel
This technique consists of isolating the stainless steel from solvents by applying a chemically inert layer of polymers to the filter body, in compliance with American and/or European standards.
Various coatings are available: PTFE, FEP, PFA and Halar©. One of the most competitive solutions is to use a Halar© coating, for which the deposition techniques have been mastered for many years. This material also offers a wide range of design options, enabling custom filters to be made.
Although ECTFE has excellent corrosion resistance, like all fluoropolymer coatings it is subject to the phenomenon of permeation. The molecules that adsorb to its surface - in this case solvent molecules - can gradually diffuse through the Halar© layer before desorbing on the other side. This chemical migration eventually causes the coating to delaminate, so it needs to be renewed regularly.
Manufacture filter housings from polymer materials
Instead of coating the stainless steel with a polymer, solid polymer filter housings can also be used. When filtration rates are low (of the order of m3/h) and the solvents used are highly corrosive with limited chemical compatibility, one option is to use solid PTFE filter housings. However, the use of this synthetic material limits the temperature and pressure conditions in which the filter housings can be used. To comply with the international codes governing the construction of pressure vessels (ASME, CODAP) to which filter housings are subject, polymer housings can only be used up to a pressure of 6 bar and a temperature of 40°C.
When the filtration equipment is larger (multi-pocket filters to retain carbon fines, catalyst retention, etc.), standard polymers (PP, PVDF) or thermosetting composites such as GRP (Glass Reinforced Plastic), also known as SVR (Glass Resin Laminate), can be used.
Legend:
1-Pure solid PTFE filter body
2-Solid PTFE filter body with antistatic treatment
Making filter housings in other metal alloys
The classic alternative to stainless steel is Hastelloy, grade C22. This nickel superalloy has mechanical properties similar to those of stainless steel. Withstanding temperatures in excess of 800°C, it is extremely resistant to corrosion but can be attacked by certain aggressive acids (formic acid, acetic acid, oleum, etc.). It can also be welded and machined, like stainless steel, to manufacture any type of filter body.
Filters produced in this way can be fully compliant with international design and construction codes.
Where the chemical-thermal compatibility of these filters is still inadequate, tantalum-coated filter bodies can be used, which combine the excellent corrosion resistance of tantalum with the mechanical properties of stainless steel, giving better performance than Hastelloy.
To find the best filter body to install when stainless steel equipment is out of the question because of the solvents used, a number of parameters need to be taken into account. As well as the technical aspects themselves, you need to consider the associated costs. In addition, there is no point in choosing filter housings whose service life would far exceed that of the production circuit for the product to be synthesised.
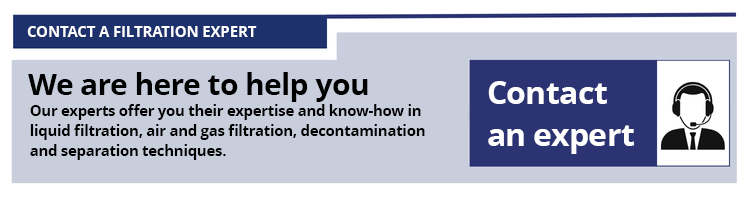