Long used in the food and drink industry, lenticular filters offer optimal, cost-effective solutions for food and drink processing. They are used in particular for applications involving small batches or moderate throughput. Each module is made up of superimposed ‘filter lenses’. What are the advantages, limitations and future developments of these filters?
Classic lenticular filters
Standard lenticular filters consist of cells, each composed of two discs of filter media isolated by a polypropylene separator. This drainage system is located at the heart of the cell, on the downstream face of the two plates, with flow taking place from the outer surface of the plates inwards. A polypropylene gasket running along the outer edge of the two discs forms a complete cell. The filter media used are of the same type as those used to make filter plates: cellulose, synthetic fibres, diatomaceous earth, silica, activated carbon, etc. Depending on the case, filtration is carried out on the surface or at depth.
The cells are stacked one on top of the other to create a lenticular module of the desired height. Adapters fixed to the central axis hold each cell in position. This geometry maximises the filtering surface in a given volume. The whole unit is placed in a watertight filtration housing, the dimensions of which depend on the diameter of the cells and their number.
Wax modules offer all the advantages of conventional filter plates, in a closed, sterile environment, to prevent external contamination and product loss. Several modules can be stacked in the same filter housing.
Expert advice :
Lenticular filters are often used in wine filtration, and at different stages (clarifying filtration, micro filtration, sterilising filtration).
Limits of conventional systems
Conventional lenticular modules have inherent design limitations.
- Because the filter media is unprotected, its integrity can be compromised during shipping, handling, installation or maintenance. After use, and for the same reasons, lenticular modules can disintegrate when removed from the filter body.
- Because the cells are so close together, they can deform or move slightly and in places come into contact with each other during sterilisation, rinsing or filtration. This ultimately reduces the effective filtration area.
- These devices cannot withstand any counter-pressure: the loose cell media can break very easily, with a counter-pressure as low as 0.05 bar. This results in tears, which divert the fluid and compromise the quality of the filtrate.
- Finally, conventional lenticular modules are not very resistant and deform under the effect of high temperatures. This sensitivity poses a problem during hot water disinfection, steam sterilisation or hot filtration operations.
New-generation lenticular filters
To optimise the capacity, reliability and robustness of lenticular filters, some manufacturers offer innovative systems based on the use of double separators, located on either side of the filter cells. The filter media is thus protected from mechanical stress, as it is encased between these two polypropylene separators, which are either snap-fitted or connected by ultrasonic welding. The outer separators, filter media discs and inner separators are placed on a rigid central polypropylene shaft. The whole assembly forms an extremely robust structure.
This arrangement prevents any risk of clogging. Thanks to the separators, the device has a maximum filtration surface throughout its working life. It is no longer possible for a cell to deform or fall, and the risk of damage to the discs is kept to a minimum. Backwash is now possible to regenerate the modules.
These new-generation lenticular devices offer a host of advantages. Their service life is longer than that of conventional filters due to better use of the filtering surface, the absence of clogging of the filtering surfaces and optimisation of the distribution of incoming fluid and drainage. The modules can be regenerated by backwashing for reuse.
The reliability of the device is also improved, thanks to its resistance to vacuum or shocks associated with back pressure, and the absence of cell deformation during operation, disinfection or hot sterilisation. This improves filtration quality, with no risk of bypass. Handling and installation are made easier by the solidity of the structure and the fact that the filter discs are now protected.
Expert advice:
These filters are available in a wide range of retention thresholds, enabling coarse to fine filtration as well as microbiological reduction.
An example: filtering glucose syrup
Some fluids used in the food industry, such as glucose syrup, contain fine particles in suspension that need to be removed. The aim is multiple: to improve the clarity of the filtered product, reduce the level of contamination, protect downstream systems, etc.
This solid contamination (e.g. heat-resistant spores) is often too great for traditional filtration using filter cartridges, as the retention capacity of these devices is limited by the available filter surface and the vacuum volume. Glucose syrup also has a high viscosity, which would require cartridge filters to be very large.
Rather than investing in expensive equipment designed to eliminate solid particles (centrifuges, filter plates, etc.), we recommend giving preference to lenticular modules, which offer a solution that is quick to install, economical and perfectly suited to this type of fluid.
In the field of edible oils, these lenticular filters can be used, for example, to carry out the final filtration and eliminate organic particles, colloids and triglycerides to prevent flocculation inside the bottles.
Looking for a lenticular filter? Contact our experts for expert advice on your choice of industrial filters.
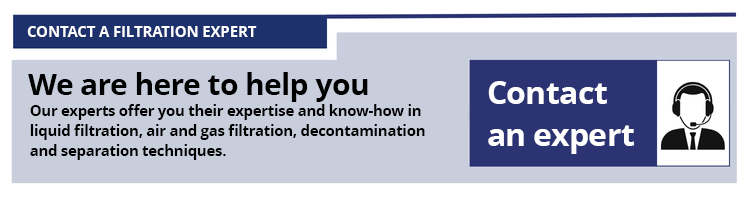