The production of fuels or polymers involves the use of industrial filters with a wide range of characteristics, which have to comply with strict regulatory standards in terms of safety and the environment. From upstream to downstream in the production chain, we need to be able to filter very different liquid and gaseous substances.
Filtration issues in petrochemicals are specific to each field
In oil refineries, the purity of the fuel produced is crucial. In the polymer industry, filtering devices are used as soon as the raw materials are introduced into the intermediate reactor, and then at each stage of the synthesis process: polymeriser, mixer, extruder, etc. The substances to be filtered have a wide range of rheologies (water, highly viscous polymer melts) and chemical compositions: polypropylene, polyester, polyethylene, polyamides, polyurethane, acetates, silicone, etc.
Expert advice :
In the polymer industry, filter cartridges often need to be made from a material capable of withstanding the extreme operating conditions present along the production chain: high pressure and temperature, corrosion from chloride ions...
Fuels: from extraction to the pump
Refineries produce diesel, petrol, heating oil, liquefied petroleum gas and paraffin. To do this, the fuel industry uses filters ‘upstream’ (water injection, protection of reverse osmosis membranes, process water) and filters ‘downstream’ (gas separation, amine reductions, catalyst beds, etc.).
In oil production, water is often used to maintain pressure and increase productivity. Particular attention must therefore be paid to its quality, whether fresh or sea water. Water can be laden with algae or plankton, silt and other sediments that can have a significant impact on plant performance.
Fuels are generally stored in large containers before being transported to their final destination via pipelines or tankers. During the storage phase, these products accumulate debris such as rust or small particles, which can cause difficulties upstream of distribution points, damage end-customer equipment and even lower the quality of the final product. They must therefore be filtered and homogenised before delivery to remove any contaminants and water they may contain. Filtration solutions based on metallic or polymer media, most often made to measure, must therefore be implemented.
The polymer industry: developing high-purity plastic fibres
Production of PET and PP fibres, PET for the manufacture of plastic bottles, thin packaging films, technical thermoplastics or X-ray films... Polymer melting processes involve several filtration stages to produce the final plastic from the raw material. To obtain high-quality fibres with low breakage and high yield, the polymer melt must be homogeneous, gel-free and without significant over-concentration. Current technologies for metallic or polymer filter media make it possible to improve performance while reducing operating costs. Metallic filter media are used, for example, in the form of pleated and cylindrical filters, capsule filters or disc filters. These filters are supplied with a variety of nozzle materials to suit all existing filter housing or tank configurations.
Expert advice :
Filter cartridges made from woven Inconel® 600 fibres offer good corrosion resistance.
See an example of isobutene filtration
See an example of filtration on a polypropylene production line
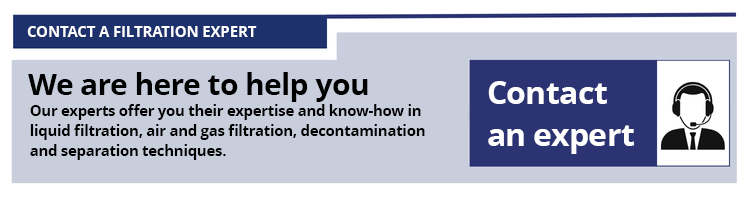