In the pharmaceutical, biotechnology, cosmetics and food industries in particular, and more generally in any industry deploying critical filtration processes, choosing the most appropriate filtration sequence is essential. The choice of filters to be deployed on the production line (which filter technologies? which dimensions? in which order?) determines not only the quality of the final product, but also the associated cost. How do you choose your filtration sequence? Why is it crucial to size your filters correctly? Are there any easy-to-use solutions for diagnosing your filtration needs?
Choosing the right filtration sequence
To determine which devices should be installed at the various filtration points in your installation, tests have to be carried out using filter discs of different materials and with given filtering characteristics. This is a lengthy and time-consuming testing process, involving a large number of flow studies and numerous qualitative and quantitative validations. Choosing the right type of filter for each filtration stage is not enough: you also need to pay particular attention to its sizing.
Find out more about filters used in the pharmaceutical industry
Focus on sizing
In these industrial sectors, correctly sizing the filters to be installed is vital, both to guarantee filtration quality and to control the associated costs.
Undersized filters will cause high initial pressure drops and will need to be replaced very frequently, resulting in high maintenance costs and potentially interrupted production. Where filters have been undersized by mistake or sometimes to reduce the initial investment, the flow rate to be treated per unit of filter surface area will be too high, causing premature filter clogging. On average, for a given flow rate, undersizing the filter by a factor of 2 will reduce its lifespan by a factor of 3. So this is far from anecdotal!
Find out more about filter clogging problems
But correctly sizing filters is a complex matter. The solution chosen will obviously depend on the use to which it will be put over time: prolonged use or, on the contrary, use restricted in time, for batch processing. Over and above these considerations, a number of other factors need to be taken into account, including the initial differential pressure, the concentration and nature of the impurities to be filtered, the space constraints associated with the installation and, of course, the flow rate of the fluid to be treated, as well as its temperature, viscosity, etc.
Portable kits, a turnkey solution
Filter selection kits are available to help you define the most appropriate filtration sequence and ultimately optimise your filtration processes.
A dedicated solution for selecting the most appropriate filtration sequence (prefilter-final filter combination) for a given fluid.
Easy to use, these selection kits give particularly reliable results. They will enable you to efficiently determine the sequence and sizing of the filters to be installed, whether you are setting up a new installation, or modernising or upgrading an existing production line. Compact, they can be deployed in even the most confined spaces.
These kits offer the following features:
- Selection of the most efficient filtration sequence
- Calculation of the optimal size of filters corresponding to the process
- Improvement of existing filtration sequences (cost, processed flow rate)
- Filtrability test
Choose a kit with a touch-sensitive tablet that is easy to use and allows wireless data transmission (wifi to a laptop or printer). The software installed on the tablet should enable you to carry out various tests (automatic or manual) and automatically calculate the filtration surface required to filter the desired volumes.
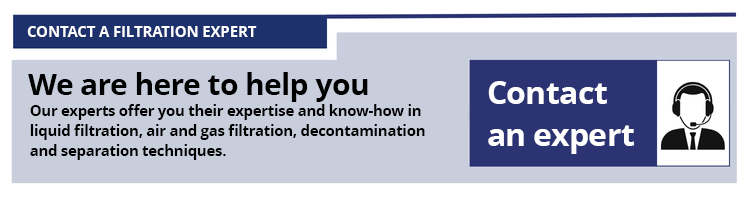