Bottles, packaging film, thermoplastics... the plastics processing industry uses filters in many of its processes. Filters are essential for producing quality plastics with good yields and controlled operating and maintenance costs.
These filtering devices must be chemically compatible with the materials - PET (polyethylene terephthalate), PP (polypropylene), cellulose acetate, nylon, etc. - and solvents to be filtered. They must also be usable over a wide range of temperatures and pressures, and be capable of handling fluids that can be very viscous. Metal filter media are excellent candidates for meeting these demanding specifications.
Plastic materials
Plastics are synthetic polymer materials made up of macromolecules. Each polymer is an assembly of small molecules, called monomers, which link together to form a long chain. The viscosity and mechanical strength of a polymer increase with the degree of polymerisation, i.e. the length of the chains.
Polymers have viscoelastic behaviour: they have both elastic properties and a viscous character. Elastic, they deform when stressed, and return rapidly to their original state once the stress is removed, a property used in industry to shape them.
In terms of viscosity, molten polymers are rheofluidifiers. At rest, they have an organised structure that is responsible for a certain resistance to flow. Flow forces the chains that make them up to orient themselves parallel to each other. As a result, they offer less resistance to flow and therefore have a lower viscosity as the stress increases.
Find out more about viscosity
Polymers can be divided into two categories according to their reaction to a rise in temperature: thermoplastics (linear polymers), which melt above a certain temperature, and thermosets (three-dimensional polymers), which cross-link and harden the first time they are heated.
Specific filtration requirements
Defects can be observed in synthesised polymers. These are generally caused by the presence of contaminants (particles, fibres or inclusions). During the process, some polymers may also gel locally, because the temperature is too high or in stagnation zones or around impurities (organic pollutants, catalysis residues, etc.). Filters are therefore essential on plastics production lines.
Candle filters
Candle filters comprise tubular metal filter elements, all of the same size, called candles, mounted vertically in parallel in a pressurised enclosure. A turntable brings the candles (made of stainless steel or other alloys) one after the other in front of the orifice from which the fluid to be filtered arrives. A flow diverter device ensures that the fluid to be treated is distributed evenly over the candles. Filters with filtration thresholds of a few micrometres to a few hundred micrometres are typically available on the market.
The filter cake, i.e. the residues and solid particles retained, gradually forms on the outside of the candles and the filtrate is collected to be injected into the rest of the circuit.
• Spark plugs have small internal spaces to avoid stagnation zones.
• This geometry provides a large filtration surface in a compact housing.
• Filter candles can be cleaned several times by backwashing or soaking in a bath and reused. They can also be replaced separately if necessary.
Expert advice :
Candle filters are available in standard formats. They can also be tailor-made to fit any camera body.
Discover an example of filtration in the polymer industry
Disc filters
Metal disc filters are used for hot filtration of highly viscous polymers. The discs, often made of stainless steel, are fixed one above the other on a shaft in a pressurised enclosure. The cake forms on the filter plates as the filtrate is drawn inwards before being recovered. The filter elements can be cleaned by vibration or washing.
These filters provide excellent control of the fluid being processed by ensuring a steady flow and outstanding retention of impurities, which are trapped within the cells of the filtering media. Their design minimizes pressure losses thanks to the large filtration surface and prevents the denaturation of the polymers being treated. Their performance is excellent, with filtration levels ranging from 5 to 40 μm. They are particularly used in the production of PET packaging films and PEEK (polyether ether ketone) electronic chips.
Filter discs are made either of woven metallic fibers arranged in different patterns or of metallic powder, depending on the application. In the first case, the selected mesh determines the filter’s operating conditions and performance.
Expert advice:
The metal powder filter discs are available in a wide range of diameters (typically 0.5 - 200 mm).
Are you facing an industrial filtration challenge? Contact our experts for expert advice on selecting the right industrial filters.
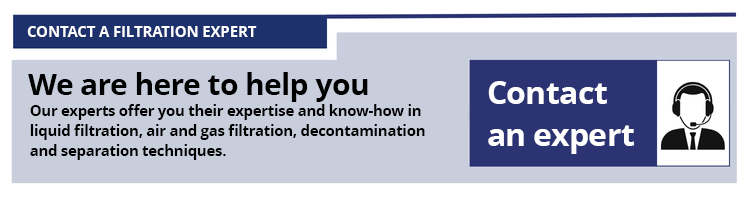