Depending on their position in the devices, the filters used in the pharmaceutical industry have different roles: essential information to know: depth filtration, surface filtration, technological and regulatory aspects.
Deep filtration
The filters used furthest upstream, for example those used for the pre-filtration of solvents during transfer to the reactors, are designed to retain elements of very variable sizes. This clarification is achieved via a filter medium of gradual density, usually made of polypropylene or nylon, which gradually retains contaminants across its entire cross-section. The retention thresholds available are generally between 0.5 and 200 µm.
Surface filtration
The elements used in the final stages of filtration, such as those designed to retain bacteria, only have to stop small concentrations of particles with a limited particle size distribution. These filters use media of various chemical compositions (polypropylene, nylon, glass fibres, polyethersulphone, Halar (ECTFE) or PTFE) which retain circulating elements of typically submicron size on their surface.
Technological and regulatory aspects
In practice, the three families of filter elements (lenticular modules, cartridges and filter bags) can be used for both types of filtration. In all cases, the various filter elements (media, solid structure and seals) must be chemically and thermally compatible with each other and with the fluid. Filters must also meet the regulatory constraints of API production.
Example of chemical compatibility :
Find out how to optimise your filtration processes in API production
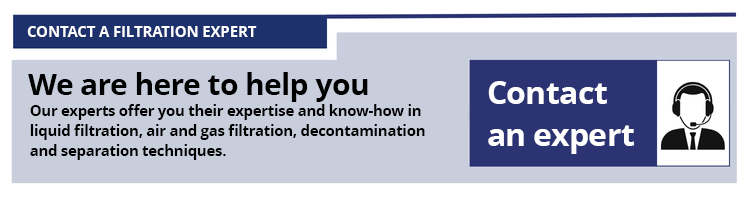