Polyamide 6.6 fibres are found in many everyday products. Examples include textiles in the broadest sense, carpets, guitar strings, in our cars (tyres, fuel tanks, etc.), electrical insulators, etc.
Nylon salt filtration: A qualitative and economic challenge
The polyamide fibre industry has evolved significantly over more than 50 years, and the polymerisation processes are well established and mastered. The industry has always looked for ways to optimise production, reduce fibre breakage and improve the inherent characteristics of the fibres. The constant challenge is to manufacture ever finer fibres that are also ever more resistant. Based on the expected production results, the studies made it possible to determine, for each fluid used, their levels of cleanliness in the ‘new’ state and to classify the size and type of contaminants generally present.
Fibre production process and filtration stages
The main basic element used in the manufacture of polyamide 6.6 fibres is nylon salt, commonly known as ‘N salt’. It comes in the form of a colourless salt solution. This salt is polymerised. This involves evaporating the water from the salt solution to form the salt into a block of polyamide paste of sufficient viscosity to pass through spinnerets, creating filaments. Once cooled, the filaments are drawn on a stretching line until the desired fibre sizes are obtained.
It has been determined that the presence of particles, even at low concentrations, can directly deteriorate the uniformity of polymer quality and alter its lifespan. Whether the contaminants are extrinsic (DI water, for example, has been identified as a ‘pollution’ vector) or originate from the process, filtration of the various feed streams has become an integral step in the polyamide 6.6 production process.
And, of course, the efficiency and reproducibility of the filters used is essential. To eliminate any uncertainty about filtration, so-called ‘absolute’ filters should be used which, in addition to being totally reproducible in their manufacture, have an efficiency of over 99.98%.
But at what threshold should we filter?
Optical microscope and X-ray spectrometry analyses revealed that the size of the particles in the fluids to be filtered varied between 0.5µm and 40µm. But the vast majority, around 90%, were between 1 and 10µm.
The main contaminants (DI water, N salt) are iron, silica and polymer elements.
It's easy to see why it's vital to check and validate filtration efficiency with your supplier. Some filters are still advertised at 1µm without any indication of the associated efficiency. The studies we have carried out in-house show that these filters (depending on the manufacture) are really absolute between 20 and 40µm, for the 1µm advertised!
But where do you integrate these filters into the process?
- The first source of contamination comes from the components used for the Nylon salt solution. In relation to the above, the ideal recommendation should be 1µm with a minimum efficiency of 99.98%.
- Contamination levels in the nylon salt solution can vary considerably. In some cases, plate filters and/or frame filters followed by disposable polishing filters are used. For highly contaminated salt solutions, we recommend that ‘depth’ filters are sequentially installed to meet the needs of improving product quality and spinning performance. This notion of ‘highly’ contaminated must be assessed in each case, but the aim of these filters is to retain insolubles such as metal oxides and other extrinsic pollution, which reduce polymerisation efficiency and therefore fibre quality.
- The make-up water must also be filtered before being mixed with the titanium dioxide at around 10µm with absolute efficiency. The slurry is then filtered to between 10 and 20µm, again with absolute efficiency. This filtration prevents the passage of large particles that could reduce the tensile strength and quality of the finished fibre.
- The ‘final’ filtration before transfer to the drawing lines typically consists of metal filtration elements pleated at high pressure depending on the decitex of the fibre produced. For the finest nylon fibres, filtration to 10 µm absolute is recommended. Fine-fibre stainless steel filtration equipment is the best guarantee of top-quality nylon fibre and the ability to produce at high speeds, with near-zero defects.
- Lastly, metal sieves are commonly used in the drawing trains to eliminate ‘large’ particles and gels that could clog the die. When operating conditions allow, particularly in terms of the pressure drops generated at the production rate, fine-fibre stainless steel media are a solution that guarantees high reproducibility and production quality.
Summary
To obtain high-quality fibres and optimise productivity, the polymer must be highly homogeneous, gel-free and free of additive agglomerates. Filtration of the primary fluids, filtration of the slurries and filtration of the molten polymers are crucial to the process. Paying particular attention to these elements helps to eliminate fibre breakage and improve fibre strength and uniformity. As well as improving the quality of the fibres produced, this also results in higher production rates and less downtime in the process - a major economic gain.
Do you manufacture polyamide fibres?
We can work with you to find ways of maximising the quality of your products and reducing your production costs, thanks to our extensive knowledge of nylon salt filtration.
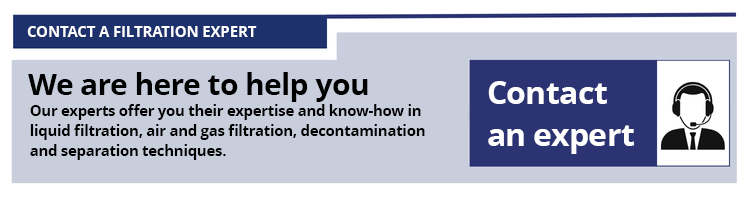