In the pharmaceutical industry, filtration and separation stages are essential. When the right filters are used, they ensure that, at the end of the chain, products (mainly medicines) are sufficiently purified and safe for patients. They also optimise the production process and limit losses of active molecules or raw materials.
The use of filters: a technological challenge
The need for filters in the pharmaceutical industry concerns not only the stages directly involved in the manufacturing process for active pharmaceutical ingredients (APIs), but also the manufacture and use of utilities (gases, liquids and steam), the cleaning and sterilisation systems in place, compressed air systems and packaging.
The temperature and pressure conditions prevailing on the production line are sometimes extreme, and the compounds used can be highly corrosive, viscous or extremely fragile. At every stage, therefore, there are numerous technological challenges to be met in order to obtain safe raw materials, utilities or finished products, within reasonable timescales and at a controlled cost.
In addition to these specifications, there are strong regulatory constraints. From the research and development stages right through to final production, the pharmaceutical industry has to meet demanding quality standards. This creates additional challenges for the installation of filters and filter housings, the filter bodies that make up the filtration process throughout product manufacture.
For example, the use of pharmaceutical water, which comes into direct contact with the product to be administered to the patient (e.g. in the manufacture of ophthalmic solutions and injectable solutions) or indirectly, is highly regulated. Their production and distribution are governed by strict standards, specific to each country, designed to guarantee their physico-chemical and microbiological properties.
To find out more about the regulatory constraints on water for pharmaceutical use and the associated filtration solutions, read the following blog article:
What are the regulatory constraints on the quality of water for pharmaceutical use?
Expert advice: Particular attention needs to be paid to the filtration of endotoxins present in water systems for pharmaceutical use. Particularly dangerous to the body, endotoxins can be eliminated using filters made from positively charged nylon membranes .
Filters, filter housings or filter skids supplied to the pharmaceutical industry must also be fully traceable, in particular by means of an individual batch number, as filters must be manufactured in clean rooms.
Filtration applications in the pharmaceutical sector
In the pharmaceutical industry, filters are used to :
- filtration of compounds produced by microbial culture, such as antibiotics
- solvent filtration for API production
- filtration of sterile gases used for pressure equalisation along the production line or to form an antibacterial barrier for storage
- filtration of autoclave vents, to protect the product from external contamination
- particles, which determine the final quality of the product and protect downstream equipment
- filtration of steam used, for example, to disinfect installations
- sterile gas filtration for fermentation and aeration agitators
- the preparation of sterile water used for diluting and dissolving medicines
- reducing the quantities of particles or bacteria upstream of the final sterilising filtration process
- sterile filtration of the final product, guaranteeing its biological quality
- sterilisation of packaging, for example by sterile vacuum filtration
Expert advice: activated carbon is used to eliminate coloured impurities produced in the reactor during the synthesis of active pharmaceutical ingredients. Rather than adding powdered carbon directly to the reactor before filtering, it is preferable to use activated carbon filters or lenticular modules with activated carbon media.
To find out more about activated carbon filters, read our blog post ‘Why use activated carbon filters in API production’.
The editors of the pemflow blog offer a number of case studies and examples of filtration solutions on their blog: filtration in the Pharma/Biotech sector.
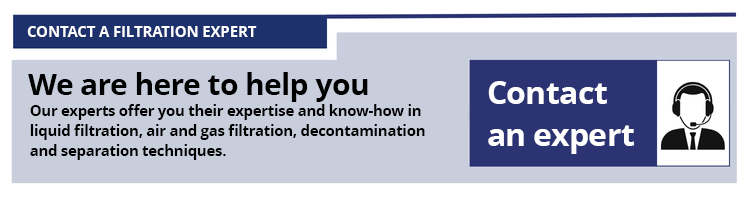